
Bendix Gear
Re: Bendix Gear
Thanks Bob. 

I've spent most of my money on women, motorcycles, and beer.
The rest of it I just wasted.
The rest of it I just wasted.
- Ken in Oklahoma
- Posts: 3182
- Joined: Tue Aug 03, 2010 5:10 pm
Re: Bendix Gear
dougie wrote:Will be looking into my Bosch starter this winter.
Looking at the microfiche, the bendix seems to have 2 bushings. Is that correct?
Yep, two bushings, and good luck getting them out. IIRC they go into what is, in effect, a blind hole. I seem to remember a lip which prevents you from devising an extractor to pull the busings forward and out (with the bendix off the shaft, of course). I ended up giving up on it, deciding that though worn, they were probably good enough.
Again IIRC the trick is to tap the inside of the busings to some thread, then use a bolt to pull them out. I also think I heard of a tool that works a little like Ed Korn's steering head bearing race remover. There is a fine lip to it which, when tightened by a bolt, will wedge itself between the bushing and the bushing behind it, and then the rearmost bushing and the lip behind it.
About that damned clip that retains the Bendix assembly itself. It took me hours to do it, trying at least two different approaches, but I finally got it. It wasn't pretty, but I got it.
I got a some of advice offline from a guy who has been in the business of rebuilding Bosch (and other) starters. Unfortunately he was turned off Boxerworks because of all the contention present. (This might have been in the days when you know who was doing his crap). But from the tone of his emails I don't think my offline correspondent would even have liked Boxerworks as it is now. He seemed to be one of those just-the-facts kind of guys who thought that Boxerworks ought to be only about posing and solving Beemer problems.
Back now to my main post: I've vowed that when the time comes that I need to overhaul or replace the bendix assembly I'll find a professional who refurbishes Bosch starters and pay him money to do it. (I sure hope I'm smart enough to keep my promise to myself.)
Oh, by the way, the starter worked just fine for me with the old bendix bushings still in place.
Ken
____________________________________
There's no such thing as too many airheads
There's no such thing as too many airheads
Re: Bendix Gear
I too had fun getting the circlip off when replacing my bendix a coupla years ago.
Seem to recall someone posting a method to compress it that made me think 'DOH!'
I can't recall the method but maybe it was something to do with a thin hose clamp??
Me no remember.
Seem to recall someone posting a method to compress it that made me think 'DOH!'
I can't recall the method but maybe it was something to do with a thin hose clamp??
Me no remember.
Lord of the Bings
- Slashsevenpig
- Posts: 38
- Joined: Tue Aug 03, 2010 7:59 am
Re: Bendix Gear
Thank you Bob, Ken, pkboxer, and ME109 for your replies.
For the general knowledge of this board, I'd like to add another method shown in one of my training manuals from way back when I attended a vocational school. It's amazing how similar an Airhead Bosch starter is to an old General Motors type. I tried upload an image I scanned from the starter section, but was unsuccessful.
The picture shows two opposing sets of pliers or locking vice-grips, holding the ring in a kind of "sandwich" between the retainer on the bottom, and a common flat washer on the top. The idea is to squeeze the ring between the retainer and the flat washer when the ring is aligned with the internal groove in the armature shaft. Thus, the ring will simultaneously pop into the internal groove of the armature shaft and the keeper. When assembly is complete, remove the flat washer. I would imagine that cleaning up any burrs on the ring would greatly help assembly, along with some kind of lubricant on the keeper.
I'm going to try any combination of ideas to get that ring back into place.
Thanks again,
Peter
For the general knowledge of this board, I'd like to add another method shown in one of my training manuals from way back when I attended a vocational school. It's amazing how similar an Airhead Bosch starter is to an old General Motors type. I tried upload an image I scanned from the starter section, but was unsuccessful.
The picture shows two opposing sets of pliers or locking vice-grips, holding the ring in a kind of "sandwich" between the retainer on the bottom, and a common flat washer on the top. The idea is to squeeze the ring between the retainer and the flat washer when the ring is aligned with the internal groove in the armature shaft. Thus, the ring will simultaneously pop into the internal groove of the armature shaft and the keeper. When assembly is complete, remove the flat washer. I would imagine that cleaning up any burrs on the ring would greatly help assembly, along with some kind of lubricant on the keeper.
I'm going to try any combination of ideas to get that ring back into place.
Thanks again,
Peter
- Ken in Oklahoma
- Posts: 3182
- Joined: Tue Aug 03, 2010 5:10 pm
Re: Bendix Gear
ME 109 wrote:I too had fun getting the circlip off when replacing my bendix a coupla years ago.
Seem to recall someone posting a method to compress it that made me think 'DOH!'
I can't recall the method but maybe it was something to do with a thin hose clamp??
Me no remember.
I tried the hose clamp thing and it didn't work for me ME 109. The problem was that the clip is round in cross section. The screw type hose clamp, mostly because of the projectiong area where the screw is, couldn't get close enough to the clip to compress it.
My second attempt was to get around that problem by creating a compressor from a section of pipe, which could snug up to the clip, and compress the pipe with the hose clamp. Because of that damned round cross section on the clip that effort failed as well. I still think it should have worked and might have worked if I'd been smart enough to refine my technique.
What we really need here is a photo essay from somebody who is smart enough to create a procedure that will work in less than an hour.
P.S. Meanwhile I'm still sore at Bosch for not making that clip rectangular in cross section. I know, it probably had to be round so the groove in the shaft would be round, so a stress riser wouldn't be created and so the end of the shaft wouldn't crack and snap off. Luckily I seldom think about it now and am almost over it.




Ken
____________________________________
There's no such thing as too many airheads
There's no such thing as too many airheads
Re: Bendix Gear
Maybe that clip was designed over at Dyna.Ken in Oklahoma wrote:
P.S. Meanwhile I'm still sore at Bosch for not making that clip rectangular in cross section. I know, it probably had to be round so the groove in the shaft would be round, so a stress riser wouldn't be created and so the end of the shaft wouldn't crack and snap off. Luckily I seldom think about it now and am almost over it.![]()
![]()
![]()
![]()
Ken
Oops...... did I say that out loud???

Garnet
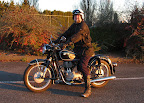
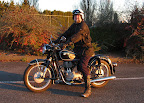
- Ken in Oklahoma
- Posts: 3182
- Joined: Tue Aug 03, 2010 5:10 pm
Re: Bendix Gear
Garnet wrote:Maybe that clip was designed over at Dyna.
Oops...... did I say that out loud???
Touche' Garnet.

Ken
____________________________________
There's no such thing as too many airheads
There's no such thing as too many airheads
Re: Bendix Gear
A tool exists. Mine are from the early part of the 20th century ('30's I would guess...) One day when I make the next "big-move" I'll pull all of my special tools out and snap pics and give up prints for everyone to enjoy; sorry, but all of that is inaccessible; its buried in storage now. 

1971 R75/5 (SWB)
If you're going to hire MACHETE to kill the bad guy, you better make damn sure the bad guy isn't YOU!
If you're going to hire MACHETE to kill the bad guy, you better make damn sure the bad guy isn't YOU!
- Slashsevenpig
- Posts: 38
- Joined: Tue Aug 03, 2010 7:59 am
Re: Bendix Gear
Hello Everyone,
I wanted to give you an update, for the benefit of anyone who is contemplating removing the Bendix drive on Bosch starters for any reason.
First, DON'T DO IT! Step back from the window ledge, and let's talk about it!
Just kidding.
It's possible to do, but it requires some patience and preparation. I first tried the ME 109 suggestion of trying to compress the retaining ring with a hose clamp, but the shape of the "worm screw" presents a flat spot to the clip when fully tightened. Plus, I would have had to pound the snots out of the end of the armature shaft to get the ring to move through the hose clamp towards the retainer.
Next, I thought about Bob's suggestion of using the Bendix drive itself to drive the retainer collar over the ring, but I wanted to save that one for last, in case the pliers produced some jaw marks on the drive teeth, or sprag-clutch housing. I tried by hand to slam the Bendix against the retainer collar, but the short distance, along with the spiral-cut teeth on the armature shaft made it difficult to generate any momentum.
About his time, I wished I had a puller, so I could try pkboxer's approach of keeping upward tension on the Bendix, freeing two hands to work the ring into the retainer. A trip to the tool store was looming large in my future.
Next, I stood the armature on end and clamped it upright in the rear bushing area in the wooden jaws of my old Workmate. I decided to try the "sandwich" method of using two pairs of pliers to squeeze the retaining ring between the retainer collar and a common flat washer. here's the steps I took:
1). With a grinding stone in a drill, I put a slight bevel in the open ends of the retaining ring. Using the same stone, I worked out any nicks in the diameter of the ring by hand. I didn't want to remove too much steel, but I wanted it to be smooth enough to pop into the retaining collar without hanging up on a nick or burr.
2). Installed Bendix dive assembly on armature shaft, followed by retainer collar, and retaining
ring. I worked the retaining ring into the best circular shape possible. Lubricated the ring, retainer, and retainer groove on the armature shaft.
3). Using a Uni-bit, I punched out the inner diameter of a 3/8" standard flat washer to 15/32" (or 381 millimeters, if my conversion is correct). For those that don't know, a Uni-bit is commonly known in the U.S. as a cone-shaped stepped drill bit with multiple cutting edges that is used to enlarge holes in light-gauge metal.
4).Placed the flat washer on the armature shaft and sandwiched the retaining ring between the flat washer, and the retaining collar. At 180 degree positions, clamped the flat washer to the retaining collar with locking pliers, commonly known as "Vice Grips" in the U.S. I did this first with only moderate locking force, and one side of the ring popped into the retaining collar. From that point, I was able to use a third set of pliers to "walk" the ring into the retainer at about 90-degree intervals, using only moderate clamping force. It actually took me about two minutes.
Remember to put a few wraps of some tape around the end of the armature, where it rides in the front bushing. It seems this surface is easily nicked. I think there are some variables that might come into play for others. Things like the condition and shape of the ring when one tries to compress it, and what types of lubricant and tools are available.
I have been reading this board for about 4 or 5 years now, and have received loads of good information. I just wanted to pass this along in case anyone else can use it.
I wanted to give you an update, for the benefit of anyone who is contemplating removing the Bendix drive on Bosch starters for any reason.
First, DON'T DO IT! Step back from the window ledge, and let's talk about it!
Just kidding.
It's possible to do, but it requires some patience and preparation. I first tried the ME 109 suggestion of trying to compress the retaining ring with a hose clamp, but the shape of the "worm screw" presents a flat spot to the clip when fully tightened. Plus, I would have had to pound the snots out of the end of the armature shaft to get the ring to move through the hose clamp towards the retainer.
Next, I thought about Bob's suggestion of using the Bendix drive itself to drive the retainer collar over the ring, but I wanted to save that one for last, in case the pliers produced some jaw marks on the drive teeth, or sprag-clutch housing. I tried by hand to slam the Bendix against the retainer collar, but the short distance, along with the spiral-cut teeth on the armature shaft made it difficult to generate any momentum.
About his time, I wished I had a puller, so I could try pkboxer's approach of keeping upward tension on the Bendix, freeing two hands to work the ring into the retainer. A trip to the tool store was looming large in my future.
Next, I stood the armature on end and clamped it upright in the rear bushing area in the wooden jaws of my old Workmate. I decided to try the "sandwich" method of using two pairs of pliers to squeeze the retaining ring between the retainer collar and a common flat washer. here's the steps I took:
1). With a grinding stone in a drill, I put a slight bevel in the open ends of the retaining ring. Using the same stone, I worked out any nicks in the diameter of the ring by hand. I didn't want to remove too much steel, but I wanted it to be smooth enough to pop into the retaining collar without hanging up on a nick or burr.
2). Installed Bendix dive assembly on armature shaft, followed by retainer collar, and retaining
ring. I worked the retaining ring into the best circular shape possible. Lubricated the ring, retainer, and retainer groove on the armature shaft.
3). Using a Uni-bit, I punched out the inner diameter of a 3/8" standard flat washer to 15/32" (or 381 millimeters, if my conversion is correct). For those that don't know, a Uni-bit is commonly known in the U.S. as a cone-shaped stepped drill bit with multiple cutting edges that is used to enlarge holes in light-gauge metal.
4).Placed the flat washer on the armature shaft and sandwiched the retaining ring between the flat washer, and the retaining collar. At 180 degree positions, clamped the flat washer to the retaining collar with locking pliers, commonly known as "Vice Grips" in the U.S. I did this first with only moderate locking force, and one side of the ring popped into the retaining collar. From that point, I was able to use a third set of pliers to "walk" the ring into the retainer at about 90-degree intervals, using only moderate clamping force. It actually took me about two minutes.
Remember to put a few wraps of some tape around the end of the armature, where it rides in the front bushing. It seems this surface is easily nicked. I think there are some variables that might come into play for others. Things like the condition and shape of the ring when one tries to compress it, and what types of lubricant and tools are available.
I have been reading this board for about 4 or 5 years now, and have received loads of good information. I just wanted to pass this along in case anyone else can use it.