Oh the horror!
Re: Oh the horror!
I'd consider pulling the flange, welding up the hole and retapping it.
Steve
Broken Arrow, Oklahoma, USA
Broken Arrow, Oklahoma, USA
Re: Oh the horror!
With the proper process, why not.Flatwins wrote:I'd consider pulling the flange, welding up the hole and retapping it.
Lord of the Bings
Re: Oh the horror!
A good solution !Flatwins wrote:I'd consider pulling the flange, welding up the hole and retapping it.
Without "proper process", nothing is going to work !ME 109 wrote:With the proper process, why not.
Even as some "processes" will be more involved than others ...
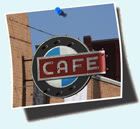
Re: Oh the horror!
Heli-coils suck – bad ! Ultimately, they break into bits ...
Or, at least, this has been my (repeated) experience.
IMO, an insert is always a better option if there is room to use one –
However, clearance may be an issue in the output flange.
I have used inserts in both alloy and steel with good success and no failures.
I have never had an insert "come out" – never.
ME109 might say: "With the proper process, why not."
and I will add, that as to insert installation, "proper process" is key !
The one advantage of an insert used in aluminum (vs in steel)
will be that the steel threads of the insert do not pull out as easily
as the original aluminum threads will,
and that the aluminum threads holding the insert will not be repeatedly stressed.
This makes the insert particularly attractive for fill and drain plugs.
Granted, the loss of aluminum threads will most often be the result
of ham-fisted wrenches who have no concept of torque
and who will assume that "tighter" is an appropriate method
to compensate for a trashed squash ring
or a technique used instead of equally torqued fasteners ...
In fact, the "tighter = better" theory might very well
be the reason for lost threads in flange screws as well, eh ?
And esp. since most will not bother with the offset adapter
needed to access and torque the flange screws properly.
Or, at least, this has been my (repeated) experience.
IMO, an insert is always a better option if there is room to use one –
However, clearance may be an issue in the output flange.
I have used inserts in both alloy and steel with good success and no failures.
I have never had an insert "come out" – never.
ME109 might say: "With the proper process, why not."
and I will add, that as to insert installation, "proper process" is key !
The one advantage of an insert used in aluminum (vs in steel)
will be that the steel threads of the insert do not pull out as easily
as the original aluminum threads will,
and that the aluminum threads holding the insert will not be repeatedly stressed.
This makes the insert particularly attractive for fill and drain plugs.
Granted, the loss of aluminum threads will most often be the result
of ham-fisted wrenches who have no concept of torque
and who will assume that "tighter" is an appropriate method
to compensate for a trashed squash ring
or a technique used instead of equally torqued fasteners ...
In fact, the "tighter = better" theory might very well
be the reason for lost threads in flange screws as well, eh ?
And esp. since most will not bother with the offset adapter
needed to access and torque the flange screws properly.
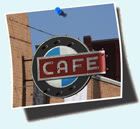
Re: Oh the horror!
Gonna use mine this weekvanzen@rockerboxer.com wrote:And esp. since most will not bother with the offset adapter
needed to access and torque the flange screws properly.


I've spent most of my money on women, motorcycles, and beer.
The rest of it I just wasted.
The rest of it I just wasted.
Re: Oh the horror!
The output flange is not easy to machine. Tapping the holes for inserts could be a problem,the material seems to be similar to the trans. shafts. Just drilling out the threads is tough.
- enigmaT120
- Posts: 3570
- Joined: Tue Aug 03, 2010 12:25 am
- Location: Falls City, OR
Re: Oh the horror!
Why not helicoil it back to the stock bolt size?
Ed Miller
'81 R65
'70 Bonneville
Falls City, OR
"Gasoline makes people stupid." -- Chuey
"I'll believe corporations are people when the State of Texas executes one." Bumper sticker
'81 R65
'70 Bonneville
Falls City, OR
"Gasoline makes people stupid." -- Chuey
"I'll believe corporations are people when the State of Texas executes one." Bumper sticker
Re: Oh the horror!
Look at vanzen's post, just 3 up, or so...enigmaT120 wrote:Why not helicoil it back to the stock bolt size?
Re: Oh the horror!
A file will barely remove material, so a cobalt drill or two may get the threads out. But after that, it sounds to me like a broken tap waiting to happen.robtg wrote:The output flange is not easy to machine. Tapping the holes for inserts could be a problem,the material seems to be similar to the trans. shafts. Just drilling out the threads is tough.
Most people who work on transmissions should have several used ones laying around, I know I do and would not mess around fixing one. The point I'm trying to make is, they are not hard to come by or expensive.
Re: Oh the horror!
Mine is free to Brad as soon as I get it loose. I'll even pay for postage!
I've always wanted to open up a transmission, and pulling the flange has been the only thing stopping me from exploring the internals of the one I have. I'm interested to see the damage done, but I can't imagine much is left besides the case.
I've always wanted to open up a transmission, and pulling the flange has been the only thing stopping me from exploring the internals of the one I have. I'm interested to see the damage done, but I can't imagine much is left besides the case.