An output flange is difficult to drill, tap, or machine ?
I don't get it ...
Yes, all of the solutions to this problem will involve tools appropriate to the task,
knowledge of those tools and the procedures to use them,
as well as some degree of personal involvement –
The only way to make it "easy" will be to hand over the cash ...
preferably to someone who has earned the skills that you will be lacking.
Oh the horror!
Re: Hard to drill, tap, or machine?
If these are the equivalent of tool steel, were they hardened after being machined? I'm just curious as to the process of making a part like this in the first place.
Re: Oh the horror!
How would you repair the threads? Would you send it out to have it annealed to a machinable condition, do the machining,vanzen@rockerboxer.com wrote:An output flange is difficult to drill, tap, or machine ?
I don't get it ...
Yes, all of the solutions to this problem will involve tools appropriate to the task,
knowledge of those tools and the procedures to use them,
as well as some degree of personal involvement –
The only way to make it "easy" will be to hand over the cash ...
preferably to someone who has earned the skills that you will be lacking.
send it back to heat treat to original hardness, regrind surfaces to true up distortion due to heat treat? Or find a used one.
Tell us how you would do it.
Re: Oh the horror!
That is what I suspected would be involved, but since I know next to nothing about metallurgy, I kept my fingers shut.robtg wrote: How would you repair the threads? Would you send it out to have it annealed to a machinable condition, do the machining, send it back to heat treat to original hardness, regrind surfaces to true up distortion due to heat treat?
Re: Oh the horror!
Yep, and answered my question in the process, too!R65 Rob wrote:That is what I suspected would be involved, but since I know next to nothing about metallurgy, I kept my fingers shut.robtg wrote: How would you repair the threads? Would you send it out to have it annealed to a machinable condition, do the machining, send it back to heat treat to original hardness, regrind surfaces to true up distortion due to heat treat?
Re: Oh the horror!
Without proper process, things will work.......to varying degrees.vanzen@rockerboxer.com wrote:Without "proper process", nothing is going to work !
With proper process, things will work as required.
My thoughts were about the hardness of the flange and what effect welding would have.
Proper process would be to know how to return the hardness to the part....if possible.
Proper process would be to know the correct filler wire to use for tig.
Tig would give the most satisfactory results as far as full fusion of weld metal to the flange, as well as the lowest heat input.
Preparing the hole by removing all thread and making the hole tapered would be needed
to assist in obtaining the highest degree of fusion. blah blah blah, etc etc.
All imo of course.
Lord of the Bings
Re: Oh the horror!
robtg wrote:
How would you repair the threads? Would you send it out to have it annealed to a machinable condition, do the machining,
send it back to heat treat to original hardness, regrind surfaces to true up distortion due to heat treat? Or find a used one.
Tell us how you would do it.
As stated in my previous post:
vanzen@rockerboxer.com wrote:If clearance for a larger screw is an issue,
and I suspect that this may be the case -
I'd then consider a threaded insert ...
but I have an install kit
which would be about the $75 price ticket of a new flange if you had to buy it.
I'll reconsider and go with frog on this one – look for a good used flange.
Send the trashed one to me.
If I did have a stripped flange lying about,
I'd not hesitate to clamp the part in the drill-press vise,
use plenty of fluid, and have a slow go at it.
Any noteworthy discussion of machining the flange, however,
will need to be predicated with the knowledge of it's specific material / hardness value.
So ... what is it ?
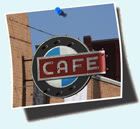
Re: Oh the horror!
.....Any discussion of machining of the flange
will need to be predicated with the knowledge of it's specific material / hardness value.
So ... what is it ?........
Who knows for sure? 4140 is used frequently for that type of application.
Hardness? --- In the "good luck running a tap through it" range.
will need to be predicated with the knowledge of it's specific material / hardness value.
So ... what is it ?........
Who knows for sure? 4140 is used frequently for that type of application.
Hardness? --- In the "good luck running a tap through it" range.

-
- Posts: 1213
- Joined: Thu Aug 26, 2010 2:11 pm
- Location: Scotland UK, 20 miles from civilisation up a dead end road!
- Contact:
Re: Oh the horror!
Been reading this for a while without butting in. Don't have any easy solution but I do have a few comments which may or may not help.
The flange appears to be made of a heavy grade steel. It is likely to be difficult to work without the appropriate tooling.
The stock bolts are metric fine thread. I'm sure helicoils and inserts can be obtained but you are unlikely to find them in stock kits. That means they are likely to be more expensive.
The clearance for the wrench to tighten the bolt is marginal in any case. It is unlikely that you will be able to fit any stock bolt with a standard sized head
Welding is probably not a good idea. The flange face needs to be kept very flat otherwise the bolts will come loose, the Morse taper that locates it to the output shaft needs to be accurate or else the flange will slip under acceleration. Localised intense heat is likely to distort the flange and render it useless. Worse, if you fit a distorted flange, you are likely to cause damage to the output shaft (not to mention the mayhem that may occur if a flange bolt works loose.
In short, I think this is one of those cases where I would counsel against any unorthodox interventions. There should be good flanges out there.
Best ofluck
Rob
The flange appears to be made of a heavy grade steel. It is likely to be difficult to work without the appropriate tooling.
The stock bolts are metric fine thread. I'm sure helicoils and inserts can be obtained but you are unlikely to find them in stock kits. That means they are likely to be more expensive.
The clearance for the wrench to tighten the bolt is marginal in any case. It is unlikely that you will be able to fit any stock bolt with a standard sized head
Welding is probably not a good idea. The flange face needs to be kept very flat otherwise the bolts will come loose, the Morse taper that locates it to the output shaft needs to be accurate or else the flange will slip under acceleration. Localised intense heat is likely to distort the flange and render it useless. Worse, if you fit a distorted flange, you are likely to cause damage to the output shaft (not to mention the mayhem that may occur if a flange bolt works loose.
In short, I think this is one of those cases where I would counsel against any unorthodox interventions. There should be good flanges out there.
Best ofluck
Rob
Re: Oh the horror!
I have no experience doing this, but thought I'd pass it on:
A good gunsmith can spot anneal hard steel parts like receivers and barrels for drilling or other machining. A carbon rod sharpened on the end is hooked to the positve side of a DC powersource and the negative is of course grounded to the work piece.
By grounding out the + carbon out on the spot to be drilled the metal is heated to a particular color. By watching the spot change color the gunsmith knows when the spot will be annealed after cooling. After the machining process he again heats the spot to a shade of red (I think) and after quenching the spot is again hardened.
I think knowing the correct shade of the correct color, requires knowing the charicteristics of the particular metal being worked on and a drive flange would be a cheap thing to experment on.
A good gunsmith can spot anneal hard steel parts like receivers and barrels for drilling or other machining. A carbon rod sharpened on the end is hooked to the positve side of a DC powersource and the negative is of course grounded to the work piece.
By grounding out the + carbon out on the spot to be drilled the metal is heated to a particular color. By watching the spot change color the gunsmith knows when the spot will be annealed after cooling. After the machining process he again heats the spot to a shade of red (I think) and after quenching the spot is again hardened.
I think knowing the correct shade of the correct color, requires knowing the charicteristics of the particular metal being worked on and a drive flange would be a cheap thing to experment on.